Exploring the Benefits of Rapid Prototype Injection Molding: A Game-Changer in Metal Fabrication
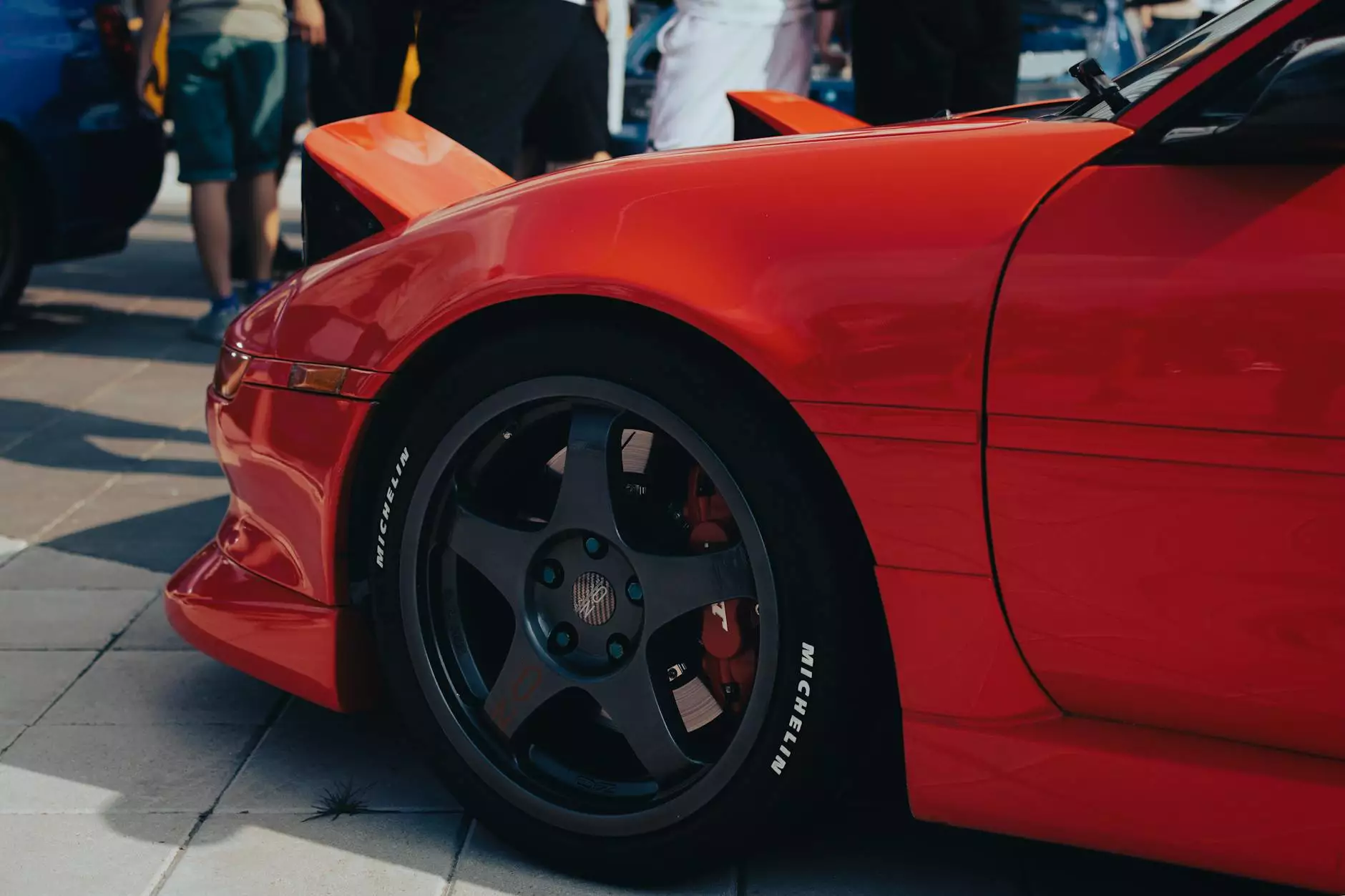
As the industrial landscape continues to evolve, businesses are increasingly looking for ways to enhance their production processes and reduce time to market. One such method that has gained remarkable traction in recent years is rapid prototype injection molding. This innovative technique not only accelerates product development but also significantly optimizes manufacturing efficiency. In this article, we will delve deep into the intricacies of rapid prototype injection molding, highlighting its advantages, technologies involved, and its impact on the performance and growth of businesses, particularly in the field of Metal Fabricators. At the forefront of this innovation is DeepMould.net, a leader in the industry.
Understanding Rapid Prototype Injection Molding
Rapid prototype injection molding is a manufacturing process that allows for the quick creation of prototypes or production-ready parts. Utilizing advanced technology and materials, this method can significantly cut down the time and cost associated with traditional manufacturing techniques. It is particularly advantageous for companies that need to iterate their designs quickly in response to market demands or customer feedback.
Key Features of Rapid Prototype Injection Molding
- Speed: The most significant advantage of this method is its rapid turnaround time. Products can go from concept to prototype in a matter of days.
- Cost-Effectiveness: Reduces costs by minimizing the number of expensive molds needed and allowing for quick design changes.
- Precision: Achieves high levels of accuracy in the production process, ensuring that final products meet stringent specifications.
- Material Versatility: Works with a wide range of materials, facilitating innovations across multiple industries.
- Design Flexibility: Rapid adjustments can be made to design specifications based on testing or customer requirements.
How Rapid Prototype Injection Molding Works
The process of rapid prototype injection molding can be broken down into several key stages:
1. Design and Modeling
The first step involves creating a digital model of the product using CAD (Computer-Aided Design) software. This model serves as the blueprint for the prototype.
2. 3D Printing the Prototype
With the advent of 3D printing technology, manufacturers can quickly produce a high-fidelity prototype from the digital model. This prototype can be tested for fit, form, and function before moving to the next stage.
3. Mold Creation
Using the validated design, a mold is created. Unlike traditional molding, which requires extensive machining, rapid prototype injection molding can utilize softer materials or 3D-printed molds to reduce costs and lead time.
4. Injection Molding Process
The final production is achieved by injecting molten plastic (or other materials) into the mold where it cools and solidifies, creating the final product. This entire process is significantly faster and more efficient than traditional methods.
The Impact of Rapid Prototype Injection Molding on Metal Fabrication
For metal fabricators, rapid prototype injection molding opens up a realm of possibilities. Let's explore how it transforms the way metal products are designed and manufactured:
Accelerated Product Development Cycle
By enabling faster prototyping, businesses in metal fabrication can bring their products to market much more quickly. This speed is essential in today's fast-paced environment where consumer preferences are constantly changing.
Improved Quality and Testing
With the ability to rapidly prototype, teams can conduct thorough testing on several iterations of a design before settling on the final version. This reduces the risk of defects in production, which can be costly and damaging to a brand's reputation.
Enhanced Collaboration and Innovation
The rapid feedback loop facilitated by rapid prototype injection molding encourages collaboration among engineers, designers, and clients. This collaborative approach fosters innovation and results in more user-centered designs.
Cost Minimization
Reducing the need for multiple expensive molds and the time associated with traditional manufacturing allows fabricators to save money. These cost savings can be redirected into further product development or marketing strategies.
DeepMould.net: Leading the Charge in Metal Fabrication Technology
As a reputed provider in the field, DeepMould.net exemplifies excellence and innovation in rapid prototype injection molding. Their commitment to quality and customer satisfaction sets them apart in a competitive landscape.
State-of-the-Art Technology
DeepMould.net employs the latest in manufacturing technology to ensure precision and efficiency. Their advanced machines can handle a variety of materials, making them versatile in meeting client needs.
Expert Team
With a team of experienced engineers and technicians, DeepMould.net ensures that every project receives the attention and expertise it requires. Their skilled personnel are adept at navigating the complexities of modern manufacturing, guaranteeing successful outcomes for every project.
Strong Client Relationships
DeepMould.net prides itself on building strong, collaborative relationships with its clients. By understanding each client's unique needs and goals, they can tailor their services to provide maximum value.
Conclusion
In conclusion, rapid prototype injection molding is not just a trend—it is a vital component of modern manufacturing, especially for businesses in metal fabrication. By embracing this innovative approach, companies like DeepMould.net are paving the way for faster, more efficient, and cost-effective production. As industries continue to evolve and consumer demands shift, staying ahead of the curve with cutting-edge manufacturing techniques will be critical. For those engaged in metal fabrication, the time to invest in rapid prototype injection molding is now.
For more information about how DeepMould.net can assist your business through rapid prototype injection molding and beyond, visit our website at DeepMould.net.