The Comprehensive Guide to Pump Cavitation: Causes, Effects, and Solutions
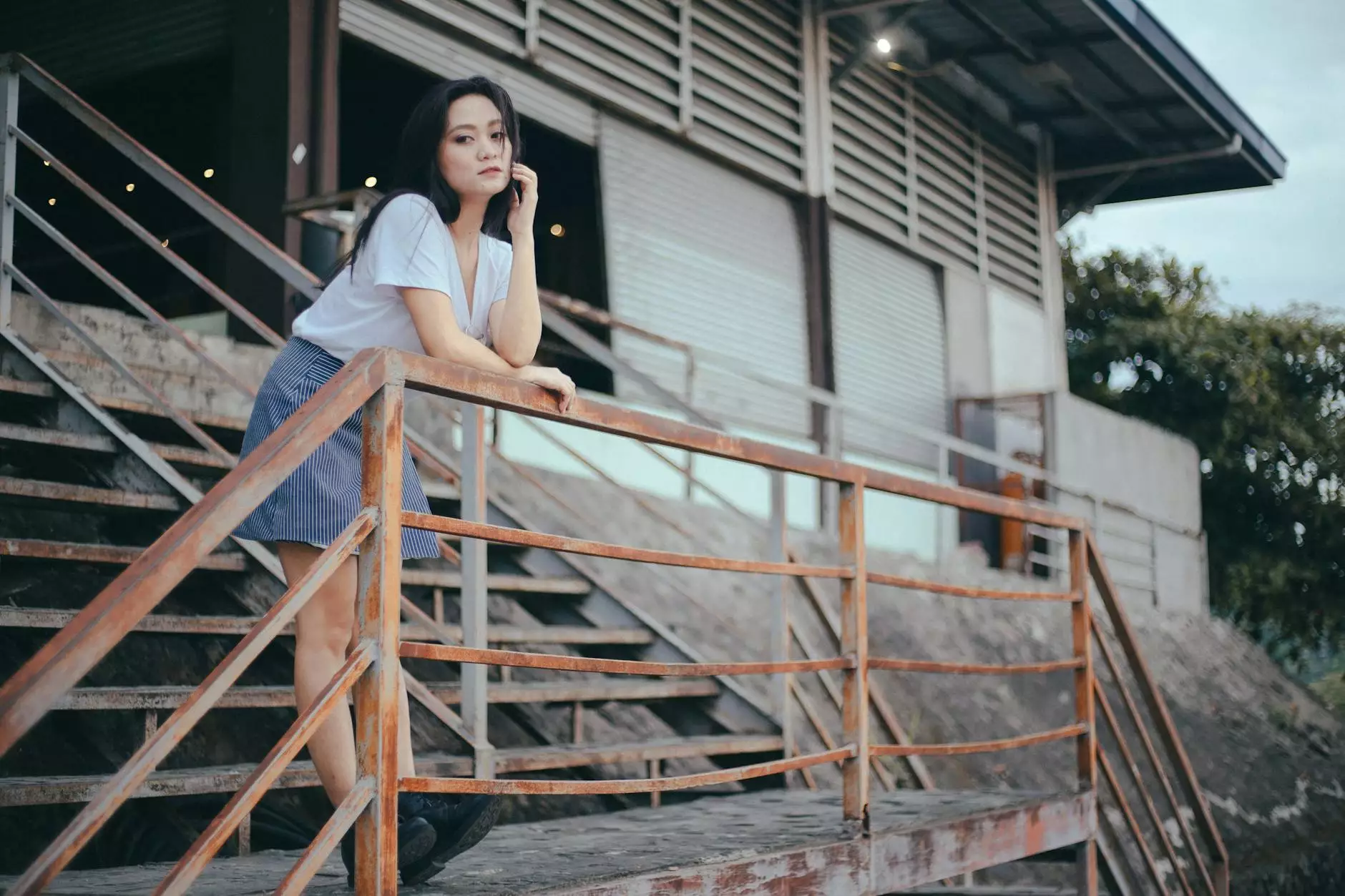
In the world of fluid dynamics and mechanical engineering, pump cavitation stands as a significant challenge that affects a multitude of industries. Understanding the intricacies of this phenomenon is essential for anyone working with pumps, whether in auto repair, farm equipment repair, or structural engineering. This extensive guide will delve into what pump cavitation is, its causes, effects on machinery, and practical solutions to mitigate its impact.
What is Pump Cavitation?
Pump cavitation occurs when vapor bubbles form in a liquid due to a drop in pressure, and subsequently implode when they reach a higher pressure area within the pump. This process can lead to significant damage to pump components and reduced efficiency. To comprehend pump cavitation, one must first understand the relationship between pressure, velocity, and the physical properties of the fluid being pumped.
Causes of Pump Cavitation
Several factors can contribute to the occurrence of pump cavitation:
- Low Inlet Pressure: When the pressure at the pump inlet drops below the vapor pressure of the fluid, cavitation is likely to occur.
- High Pump Speed: Increasing the speed of the pump can lead to higher velocities that might reduce the pressure in certain areas, promoting cavitation.
- Improper Pump Sizing: Using a pump that is too large or too small for the application can create turbulent flow patterns that contribute to undesired pressure drops.
- Liquid Properties: The temperature and vapor pressure of the fluid can affect cavitation. Hotter fluids have higher vapor pressures, increasing the risk of cavitation.
- Viscosity Variations: Fluids with different viscosities can affect flow characteristics and, consequently, the chances of cavitation.
Effects of Pump Cavitation
The effects of pump cavitation can be severe, leading to critical failures in machinery and systems. Here are some of the notable impacts:
- Physical Damage: The implosion of vapor bubbles creates shock waves that can erode and damage the surface of the pump components, particularly the impeller and volute.
- Reduced Efficiency: Cavitation leads to a drop in the flow rate and pressure, making the pump operate less efficiently and increasing energy consumption.
- Increased Maintenance Costs: Frequent repairs or replacements due to wear and damage caused by cavitation can result in significant maintenance expenses.
- System Downtime: Pump failures caused by cavitation can lead to unscheduled downtime, impacting production and overall operational efficiency.
Identifying Pump Cavitation
Recognizing the signs of pump cavitation early can help in taking timely actions to prevent further damage. Common symptoms include:
- Unusual Noise: A distinct grinding, rattling, or "marbles in a blender" sound can indicate cavitation.
- Vibration: Increased vibration levels in the pump can signify cavitation, often requiring immediate attention.
- Decrease in Performance: A noticeable drop in performance metrics, such as flow rate and pressure, can point to cavitation problems.
- Visual Inspection: Erosion or pitting on the impeller or other components during maintenance checks can provide visual clues to cavitation damage.
Preventing Pump Cavitation
Preventative measures are crucial for mitigating the risks and impacts of pump cavitation. Consider the following strategies:
- Ensure Adequate Inlet Conditions: Maintain proper inlet pressure by adjusting the system layout or using pumps with appropriate specifications to reduce the risk of low pressure.
- Choose the Right Pump: Selecting a pump that matches the application requirements is essential to avoid oversized or undersized issues.
- Control Pump Speed: Using variable frequency drives (VFDs) can help regulate pump speeds based on actual demand, reducing the likelihood of cavitation.
- Install Suction Stabilizers: These devices can help smooth out flow upstream, preventing sudden drops in pressure that lead to cavitation.
- Regular Maintenance: Conduct routine inspections and maintenance on pumps to identify wear and tear that may contribute to cavitation risks.
Handling Pump Cavitation
If cavitation is already occurring, swift action is necessary to mitigate damage. Here are some steps to handle the situation:
- Assess the System: Analyze the system configuration to identify any design flaws or operational issues that may have led to cavitation.
- Reduce Pump Speed: Lowering the pump speed can sometimes alleviate the effects of cavitation, especially in variable frequency drive-controlled systems.
- Inspect and Repair: Check for physical signs of damage and replace affected components before cavitation leads to catastrophic failures.
- Consider Upgrades: Evaluate whether the current pump system meets the necessary requirements, and consider upgrading to a more suitable model if needed.
Real-World Applications and Implications
The implications of pump cavitation are far-reaching, impacting several sectors. In auto repair, for instance, effective cooling systems in engines can be compromised by cavitation. Understanding and addressing these issues can enhance the vehicle's reliability and performance.
In the realm of farm equipment repair, agricultural pumps used for irrigation are particularly vulnerable to cavitation, which can diminish water delivery efficiency. Preventive maintenance and appropriate pump selection are key to ensuring optimal agricultural operations.
In structural engineering, the use of pumps in various applications such as concrete mixing and transportation can face challenges from cavitation too. Ensuring that systems are designed with cavitation risks in mind is essential for project success.
Conclusion
In conclusion, pump cavitation poses a significant threat to the efficiency and longevity of pump systems across various industries, including auto repair, farm equipment repair, and structural engineering. Understanding its causes, recognizing the signs, taking preventative measures, and addressing issues promptly can lead to enhanced performance and reduced costs. By prioritizing education and awareness of cavitation, professionals in these fields can ensure reliable and efficient operations.
Final Thoughts
Investing time in understanding pump cavitation pays dividends in creating robust systems capable of withstanding the challenges that arise in fluid transport. For further information and expert assistance, consider reaching out to professionals at Michael Smith Engineers, who specialize in addressing such critical issues.